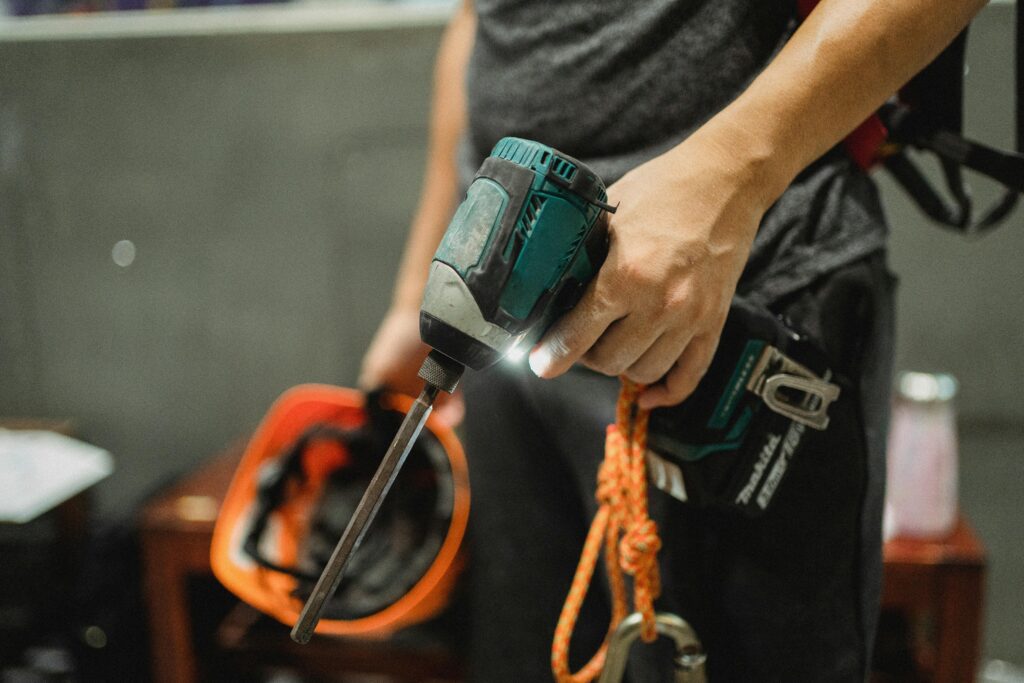
Industrial equipment is the backbone of numerous operations, from manufacturing and processing to energy production and infrastructure. To maintain peak performance, reliability, and safety, comprehensive plant support services are essential. These services encompass a wide range of activities, including preventative maintenance, corrective repairs, and asset management. By implementing effective plant support strategies, businesses can optimize productivity, minimize downtime, and extend the lifespan of their critical equipment.
Many plant support service providers, such as Murphy Rigging, offer specialized services to guarantee the smooth running of the equipment throughout the year. As experts in plant support, we feel it would be beneficial to share more about the ways that proactive industrial equipment maintenance can benefit your business.
Understanding Plant Support
Plant support refers to a spectrum of services in charge of ensuring, refurbishing, and enhancing industrial equipment. Such support ranges from basic maintenance schedules and breakdown services in addition to the upgrade or installation of systems and equipment. These services also include heavy equipment moving as facilities evolve and grow. In this way, the plant support services approach guarantees not only the operation of industrial equipment but also its proper performance and efficiency.
Murphy Rigging understands that plant support goes beyond being a service that a company provides; it’s a promise of reliability in the support for your business. Whether it involves the installation of initial equipment or the ongoing maintenance of in-production equipment, we take it upon ourselves to provide comprehensive service that ensures your facility operates as consistently and efficiently as possible, free from any breakdowns.
The Importance of Industrial Equipment Maintenance
Industrial equipment is the lifeblood of many businesses. It drives production, increases efficiency, and ensures product quality. However, like any complex machinery, industrial equipment requires regular maintenance to function optimally. Preventive maintenance is a proactive approach that involves regular inspections, cleaning, and lubrication to identify and address potential issues before they escalate into costly breakdowns. By investing in a robust maintenance program, businesses can significantly improve equipment reliability, reduce downtime, and extend the lifespan of their assets.
Here’s why investing in regular maintenance can benefit your plant:
1. Reduced Downtime: Regular equipment breakdowns shut down entire operations and render them ineffective. These are some of the frequent failures that need proper maintenance to reduce probable chances that might affect production, thereby increasing time and reducing the plant’s ability to meet production deadlines.
2. Cost Savings: While maintenance might incur additional expenses, maintenance saves money in the long run. Routine assessment and maintenance eliminate cases of major equipment failure that would need costly overhauls or replacements.
3. Safety and Compliance: If equipment malfunctions, employees are in danger of injury, and a threat to life arises. Industrial equipment maintenance covers aspects such as the safety of the relevant equipment and its compliance with standard industry regulations.
4. Improved Efficiency: Well-maintained equipment tends to give better results. Through proper plant support, there is an increase in the efficiency of the machinery used in production since they consume less energy, hence increasing the quality of production.
By prioritizing industrial equipment maintenance, businesses can reap numerous benefits, including increased productivity, reduced operational costs, enhanced safety, and improved product quality. Well-maintained equipment not only contributes to the overall success of the organization but also ensures the well-being of employees and the environment.
Key Components of a Plant Support Program
A comprehensive plant support program is essential for ensuring the optimal performance and longevity of industrial equipment. Such a program typically includes several key components, including:
Preventive Maintenance
Preventive maintenance is a proactive approach to equipment care. By conducting regular inspections, cleaning, lubrication, and minor adjustments, businesses can significantly reduce the risk of unexpected breakdowns. This proactive strategy helps maintain optimal equipment performance, extend asset lifespan, and minimize costly emergency repairs.
Emergency Repairs
Despite diligent preventive maintenance, equipment failures can still occur. A reliable plant support provider should offer prompt emergency repair services. By responding quickly to breakdowns, businesses can minimize downtime, reduce production losses, and maintain operational continuity.
Equipment Installation and Upgrades
As technology advances and operational needs evolve, businesses may need to install new equipment or upgrade existing systems. A skilled plant support team can handle these projects efficiently, ensuring seamless integration and optimal performance. Proper installation and configuration are crucial to prevent future issues and maximize the benefits of new equipment.
Safety Inspections
Safety is a paramount concern in any industrial setting. Regular safety inspections are essential to identify and address potential hazards, ensuring the well-being of employees and the protection of equipment. By adhering to industry safety standards and regulatory requirements, businesses can mitigate risks and prevent accidents.
By implementing a comprehensive plant support program, businesses can significantly enhance equipment reliability, optimize operational efficiency, and minimize downtime. Investing in preventive maintenance, emergency repair services, equipment installation and upgrades, and safety inspections is crucial to ensuring the long-term success and sustainability of industrial operations.
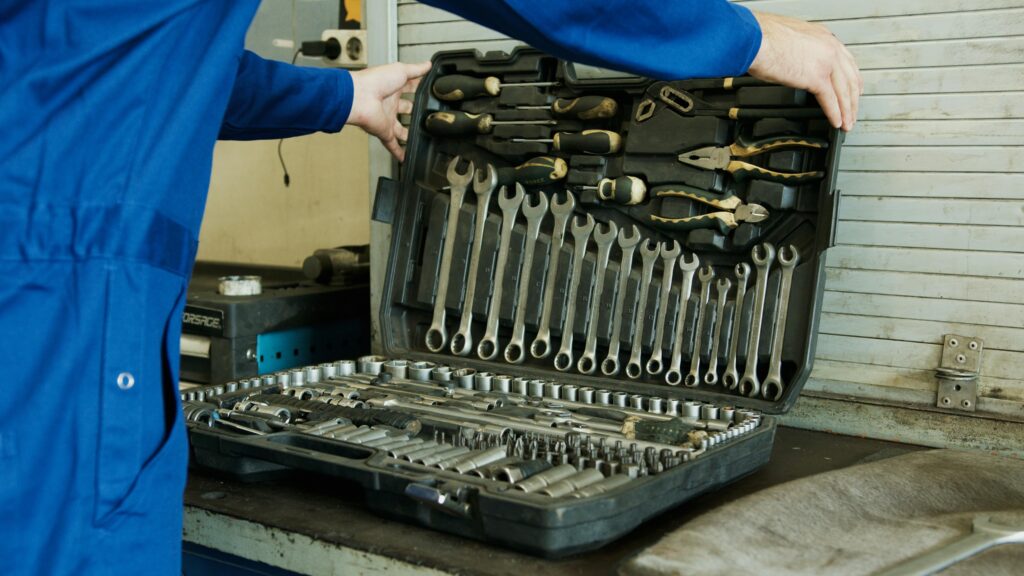
A Comprehensive Approach to Industrial Equipment Maintenance
Murphy Rigging is widely recognized as a welding fabrication company that delivers exceptional services across many industries. Whatever the industry and whatever the project, Murphy Rigging brings precision, safety, and reliability to the project. Some of the key ways in which we stand out include:
Effective industrial equipment maintenance is critical to ensuring optimal performance, longevity, and safety. A well-structured maintenance program involves several key steps:
Initial Assessment: A thorough initial assessment is the foundation of any maintenance strategy. This involves a detailed evaluation of the equipment’s current condition, including physical inspections, performance analysis, and a review of historical maintenance records.
Routine Inspections: Regular inspections are essential for identifying potential issues early on. By visually inspecting components and conducting functional tests, maintenance technicians can detect and address problems before they escalate into major failures.
Lubrication and Cleaning: Proper lubrication and cleaning are crucial for maintaining optimal equipment performance. Regular lubrication reduces friction, prevents wear, and extends the lifespan of components. Cleaning removes contaminants that can hinder performance and lead to premature failure.
Component Replacement: Over time, equipment components experience wear and tear. Timely replacement of worn or damaged components is essential to prevent unexpected breakdowns. A well-planned replacement schedule can help maintain equipment reliability and minimize downtime.
Performance Monitoring: Continuous monitoring of equipment performance is vital for identifying trends and predicting potential failures. By tracking key performance indicators such as energy consumption, output quality, and operating temperatures, maintenance teams can proactively address issues and optimize equipment efficiency.
Documentation and Reporting: Detailed documentation of all maintenance activities is essential for tracking equipment history, identifying recurring issues, and planning future maintenance schedules. Accurate records can also aid in regulatory compliance and insurance claims.
By implementing a comprehensive maintenance program that incorporates these key elements, businesses can significantly improve equipment reliability, reduce operational costs, and enhance overall productivity.
Why Choose Murphy Rigging for Your Plant Support Needs?
Murphy Rigging has a proven track record of providing exceptional plant support and industrial equipment maintenance services. Our experienced technicians and comprehensive range of services ensure optimal equipment performance and minimize downtime.
Key Benefits of Choosing Murphy Rigging:
Comprehensive Services: We offer a comprehensive suite of plant support services, including preventive maintenance, predictive maintenance, corrective repairs, emergency breakdown services, equipment installations, and upgrades.
Expert Technicians: Our highly skilled technicians have the expertise to handle a wide range of industrial equipment, from simple machinery to complex automated systems.
Rapid Response: We understand the critical nature of downtime. Our team is committed to providing prompt and efficient service, minimizing disruption to your operations.
Tailored Solutions: We recognize that every business has unique needs. Our customized approach ensures that our services align with your specific requirements and goals.
Preventive Maintenance: By implementing a proactive maintenance strategy, we can identify and address potential issues before they escalate into major breakdowns, reducing downtime and extending equipment lifespan.
Predictive Maintenance: Our advanced maintenance techniques enable us to predict potential failures and schedule maintenance proactively, optimizing resource allocation and reducing maintenance costs.
Safety Compliance: We prioritize safety and adhere to industry standards and regulations to ensure a safe working environment for your employees.
By partnering with Murphy Rigging, you can optimize your equipment’s performance, extend its lifespan, and improve overall operational efficiency.To learn more about our plant support services, contact our experts today.