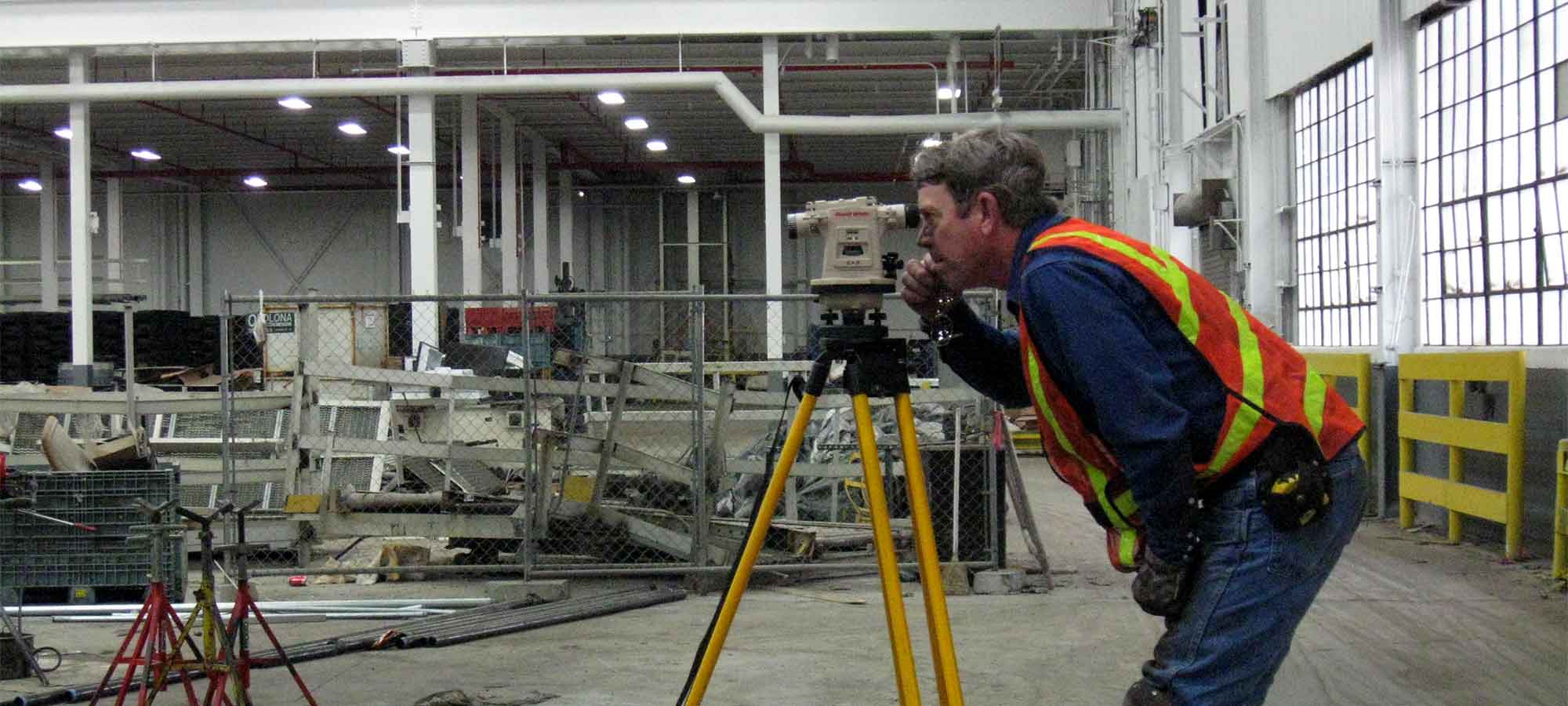
Precision alignment of machinery involves more than just a technical process; it involves a delicate balance of art and science. It’s about ensuring that every component of a machine is precisely positioned to function optimally. When done correctly, it can significantly enhance machine performance, reduce downtime, and extend equipment life. However, when machinery precision alignment is done incorrectly, it can lead to a host of problems, from reduced efficiency to catastrophic failures.
Because of the importance of precision machinery alignment, it’s important to understand some of the most important aspects of alignment to help you better maintain your investment. In this article, we will delve into the intricacies of machinery precision alignment, exploring techniques like soft foot correction, thermal expansion considerations, and vibration analysis.
The Foundation of Precision: Soft Foot Correction
Understanding Soft Foot
Soft foot is a common mechanical issue that occurs when one or more feet of a machine are not fully supported on its foundation. This uneven support can lead to a host of problems, including:
- Misalignment: Soft foot can cause the machine’s components to become misaligned, leading to reduced accuracy and efficiency.
- Increased Vibration: Uneven loading can induce excessive vibration, which can damage machine components and reduce their lifespan.
- Premature Wear: Increased stress on bearings, shafts, and other components can accelerate wear and tear, leading to frequent breakdowns and costly repairs.
Reduced Machine Life: The cumulative effects of misalignment, vibration, and premature wear can significantly reduce the overall lifespan of the machine.
The Correction Process
Correcting soft foot involves a precise and meticulous process that requires specialized tools and expertise. The general steps involved include:
- Identifying Soft Foot: Technicians use dial indicators to measure the vertical movement of each machine foot. Any significant variation in movement indicates soft foot.
- Shimming: Shims, typically made of steel or brass, are placed under the machine feet to level the machine and ensure even contact with the foundation.
- Re-Measuring: After shimming, the machine is re-measured to verify that the soft foot has been corrected.
- Final Alignment: Once the soft foot is corrected, the machine is aligned using precision alignment techniques to ensure optimal performance and longevity.
By addressing soft foot issues promptly and effectively, organizations can significantly improve the reliability, efficiency, and lifespan of their machinery.
The Impact of Temperature: Thermal Expansion
Understanding Thermal Expansion
Thermal expansion is a natural phenomenon that occurs in all materials when they are subjected to heat. As the temperature of a material increases, its molecules vibrate more rapidly, causing the material to expand in all directions. In the case of machinery, this expansion can cause components to shift out of alignment, leading to a variety of problems.
Common issues caused by thermal expansion include:
- Reduced accuracy: Misaligned components can affect the precision of a machine, leading to inaccurate measurements or production errors.
- Increased wear: Misalignment can cause increased friction and stress on machine components, leading to accelerated wear and tear.
- Reduced efficiency: Misaligned components can reduce the efficiency of a machine, leading to increased energy consumption and higher operating costs.
- Catastrophic failure: In severe cases, thermal expansion can lead to catastrophic failure of machine components, resulting in costly downtime and potential safety hazards.
To mitigate the effects of thermal expansion, engineers and technicians can use a variety of techniques, including:
- Designing machines with thermal expansion in mind: By carefully considering the materials used and the design of the machine, engineers can minimize the impact of thermal expansion.
- Using thermal expansion compensation devices: These devices can help to counteract the effects of thermal expansion, ensuring that machine components remain aligned.
- Implementing proper maintenance procedures: Regular maintenance and inspection can help to identify and address potential issues related to thermal expansion.
By understanding the principles of thermal expansion and taking appropriate measures to mitigate its effects, millwrights, engineers, and technicians can help to ensure the optimal performance and longevity of machinery.
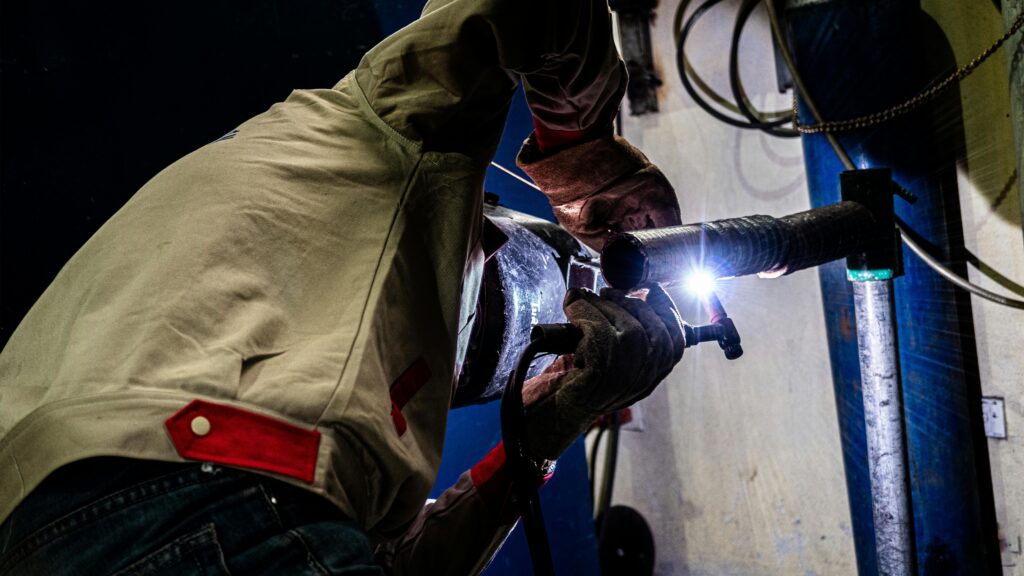
Fine-Tuning Performance: Vibration Analysis
Understanding Vibration Analysis
Vibration analysis involves measuring the vibrations produced by a machine while it is operating. These vibrations can be caused by a variety of factors, including mechanical imbalances, misalignment, bearing defects, and structural problems. By analyzing the frequency, amplitude, and phase of these vibrations, technicians can identify the root cause of the problem.
Benefits of Vibration Analysis
- Predictive Maintenance: By identifying potential problems early, vibration analysis can help prevent costly breakdowns and downtime.
- Improved Efficiency: Well-maintained machinery operates more efficiently, reducing energy consumption and operational costs.
- Enhanced Reliability: By addressing issues promptly, vibration analysis can improve machine reliability and uptime.
- Increased Safety: Early detection of potential failures can help to prevent accidents and injuries.
Common Applications of Vibration Analysis
- Rotating Equipment: Vibration analysis is commonly used to monitor the health of rotating equipment such as motors, pumps, fans, and compressors.
- Reciprocating Equipment: Vibration analysis can also be used to monitor the health of reciprocating equipment, such as internal combustion engines and hydraulic pumps.
- Structural Monitoring: Vibration analysis can be used to monitor the structural integrity of buildings, bridges, and other structures.
By incorporating vibration analysis into a comprehensive maintenance program, organizations can significantly improve the reliability and efficiency of their machinery.
Working With Machinery Precision Alignment Experts
Precision machinery alignment is a critical aspect of maintaining optimal machine performance. By understanding the nuances of techniques like soft foot correction, thermal expansion considerations, and vibration analysis, you can ensure that your equipment runs smoothly and efficiently.
If you’re looking for expert rigging and millwright services to handle your machinery alignment needs, consider Murphy Rigging. Our skilled technicians have the knowledge and experience to deliver machinery precision alignment solutions tailored to your specific requirements. Whether you need machinery movers or simply want to improve the performance of your existing equipment, our rigging services and millwright services can help.